This is a Guest Post by Priyam G. Agrawal, Country Head of India for HAMA: With over 9,300 active product lines, Hama is one of the leading accessory companies around the globe, specialising in a number of areas including gaming accessories, iPhone and Mac accessories, photo, digital, audio-visual, multimedia, mobile phones and optics to appeal to the tech savvy generation.
Quality tests are at the final stage of product manufacturing to ensure that stakeholders receive the best quality products. Attached to quality testing is ‘quality assurance’ which refers to the process of ensuring that a company’s product(s) is of the highest possible quality for customers. There are various techniques involved in this process and every company has a different standard for this; however, certain procedures remain standard across all players because they are mandated by the authorities concerned. Generally speaking, a quality inspection involves measuring, examining, testing, or gauging various characteristics of a product and comparing those results with specified requirements to determine whether there is conformity.
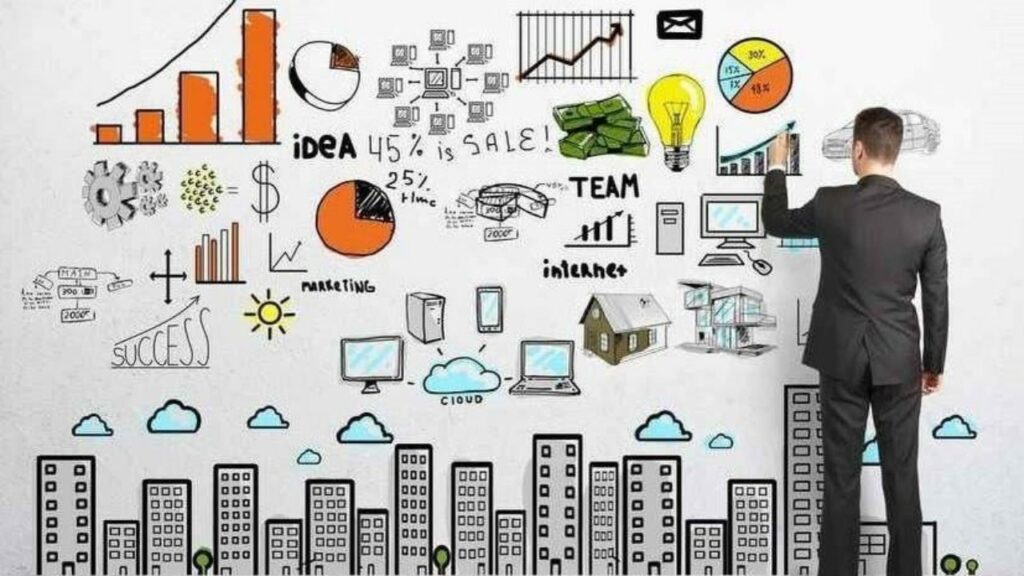
Certification marks on a commercial product are usually called a mark of validity or an assurance of the fact that the manufacturer has tested the product and that it meets the given quality standard. It also helps to specify the location of the origin, materials of construction, mode of production, characteristics of the good, etc. Some of these marks are mandatory while some are advisory. A certification mark certifies the nature or origin of the goods or the services to which it has been applied. A special body which is called as Bureau of Indian Standards (BIS), which comes under the aegis of the International Organisation for Standardisation(ISO standards), governs all industrial standardization and industrial product certifications in India.
There are various stages of product testing that are cued & planned in advance; the procedures however are altered in accordance with the products. Testing environment according to the product testing guidelines is created and to choose the standards to which will compare the results of the test, which will help to determine whether the product performs its intended function and whether it does so satisfactorily.
All companies want to ensure their products work correctly and meet their standards for quality. This applies to new products that are under development and existing products that must undergo quality testing. Product testing is a critical part of the product development process and is sometimes required legally or to work with another company. There are many different types of tests for evaluating various aspects of products such as A Highly Accelerated Life Test (HALT); Vibration & Shock Test; Environmental Stress Screening (ESS); Accelerated Weathering Tests; Thermal & Humidity Testing; and Mechanical Endurance Test among others. These tests primarily take into consideration the lifecycle of the product, its long-term and short terms durability on physical impact, and performance across various environmental conditions.
Product testing is important for companies across a wide variety of sectors as it helps them accomplish a range of goals from improving a product to discovering and correcting design issues with new products to verifying compliance. Quality testing helps in increasing customer loyalty, gaining repeat business, getting new customers from referrals, maintaining & improving position in the market, improving safety, reducing liability risks, and contributing to overall positive branding of your product. Quality control in manufacturing can be a little tricky. Often, it is done at the end of the production process, only catching defects after the whole production is done.
Effective quality control is more involved and should include two levels: Operators monitor the manufacturing process and ensure that there is little variation. Engineers routinely monitor the product design for issues. When a problem is found, it is immediately fixed. By monitoring products at the end of production as well as reviewing the products’ design, companies can solve problems more efficiently, saving time and money. It is to be noted however that, quality testing and product inspection address different quality concerns; product testing, often known as lab testing, typically involves testing a product against a specific standard or regulation in a certified laboratory. Whereas product inspection often involves checking a random sample of an order for compliance with a buyer’s requirements and specifications.
Tech is playing a stronger role in making sure that business objectives are being met. Since the human element of business, which previously made up for the lack of product/service quality, has been reduced, tech is helping to overcome the lack of physical interactions during this time. Changing customer desires have therefore caused the Quality Assurance discipline to evolve into Quality Engineering (QE). This encompasses all business processes and customer experience stages to ensure the absence of quality irregularities between each stage. In the coming times, quality management will need to adapt to support digital transformation, shifting ‘left’ to helping organizations design and de-risk systems and processes, and helping organizations translate big data into real value in terms of preventing failure and solving complex problems.