Northwestern University chemists have developed a non-toxic, resource-efficient, solvent-free method for breaking down plastic waste by utilizing moisture from the air. Their process employs an inexpensive catalyst to break down polyethylene terephthalate (PET), a commonly used plastic in polyester products. The broken PET fragments are then exposed to ambient air, where trace moisture converts them into monomers, the fundamental building blocks of plastic. These monomers can then be recycled into new PET products or upcycled into more valuable materials. This breakthrough addresses the shortcomings of current recycling methods, which often require high temperatures, energy-intensive processes, and toxic solvents.
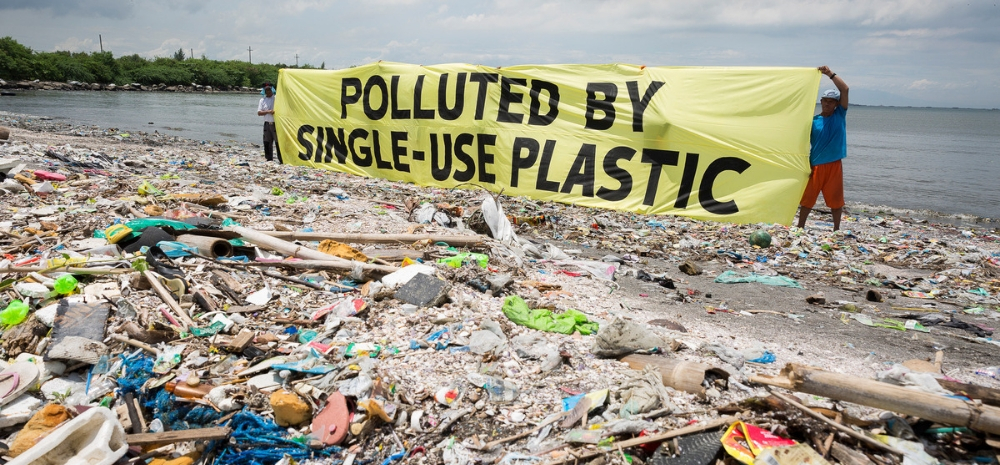
Revolutionizing Plastic Recycling: A Solvent-Free, Air-Moisture-Based Solution
The United States recycles only 5% of its plastics, highlighting an urgent need for more efficient recycling technologies. Current methods mostly downcycle plastics into lower-quality products, whereas Northwestern’s innovative approach ensures clean and selective recycling. By leveraging air moisture, the process eliminates the need for additional solvents and reduces energy consumption, making it both environmentally friendly and practical for large-scale application. Researchers emphasize that this method offers a sustainable solution to the global plastic waste crisis by minimizing toxic byproducts and enhancing recyclability.
PET plastics, commonly found in beverage bottles and food packaging, contribute significantly to pollution due to their durability and resistance to natural decomposition. Traditional recycling techniques rely on expensive, toxic catalysts and require separating recycled materials from solvents, which is costly and inefficient. Previous research by Northwestern’s Marks group pioneered solvent-free catalytic processes, and the new study extends this work by using moisture from air instead of additional chemicals.
Breakthroughs in Plastic Recycling: Efficient PET Breakdown and AI-Optimized HDPE Reuse
Using a molybdenum catalyst and activated carbon, researchers efficiently broke down PET plastics in just four hours, recovering 94% of the valuable monomer terephthalic acid (TPA). The only byproduct, acetaldehyde, is a valuable industrial chemical, making the process nearly waste-free. Additionally, this method selectively targets polyesters, eliminating the need for pre-sorting plastics—a significant advantage for industrial recycling. Real-world tests on plastic bottles, textiles, and mixed plastic waste confirmed the method’s effectiveness.
Meanwhile, chemists at Cornell University have developed a machine-learning model, PEPPr, to optimize high-density polyethylene (HDPE) recycling. By predicting the properties of recycled materials, PEPPr enables manufacturers to reduce material use while maintaining quality, making recycling more economically viable. Together, these advancements pave the way for a cleaner, more sustainable future in plastic waste management.
Summary:
Northwestern University developed a solvent-free method using air moisture to break down PET plastics into recyclable monomers. The process is efficient, environmentally friendly, and eliminates toxic byproducts. Cornell researchers created PEPPr, an AI model optimizing HDPE recycling. These innovations enhance sustainability, reduce waste, and improve plastic recycling efficiency.